We now have a reliable, future-proof solution that can compete with a brand-new press line. By bringing in AP&T to upgrade our equipment, we have nearly halved our cycle times,” says Tomas Lidbacken, CEO of PVI Esskå in Landeryd, Sweden.
PVI Esskå in Landeryd is a well-established sub-supplier to the Swedish automotive industry. They mainly manufacture chassis and body parts for heavy trucks.
Their relationship with AP&T stretches back to the 1980s. Through the years, a number of AP&T’s hydraulic presses and production lines were installed in the PVI Esskå facility, pretty much all of which are still operational.
“The mechanical parts in our presses are practically immune to wear and tear, but the control system and other electronics eventually become outdated. To prevent unplanned downtime and ensure long-term spare part accessibility, we recommend that customers of older production lines look to see what can be improved,” says Dan Barvö, Key Account Manager at AP&T.
And that’s how the current upgrade came about in 2019. The fully automated production line that’s been in operation since the year 2000, contains three 500-ton hydraulic presses and various linear robots.
“We looked over the state of the equipment and its performance and suggested measures that would minimize the risk of future production downtime as well as provide a more efficient process,” says Barvö.
The recommendation presented to PVI Esskå included a rebuild of the line control systems and replacement of all its automation. It was a substantial investment, but far cheaper than purchasing an entirely new line.
The decision to proceed was made at the start of 2020.
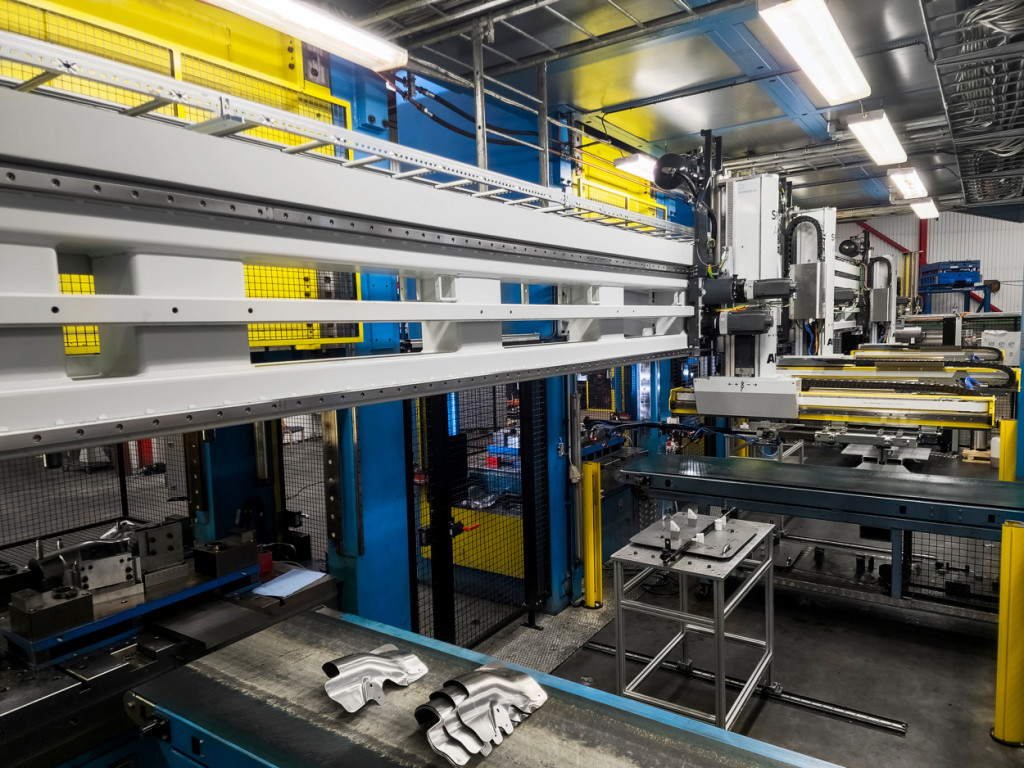
The fully automated press line manufactures chassis and body parts for heavy trucks. The upgrade increased production capacity by about 500 hours/year.
“We felt very secure that we were making the right decision. A few years ago, AP&T did a similar rebuild of one of our other lines and the results thoroughly exceeded our expectations. With the investment we are now making, we are counting on being able to increase our production capacity by about 500 hours a year,” says Tomas Lidbacken.
The goal was to have all equipment in place by the end of the vacation period in the summer of 2022. The line was shut down at the beginning of July. About four weeks later, the installation was complete, and the upgraded line could be restarted.
“Everything went according to plan. We exchanged all control systems and operator panels and installed three new SpeedFeeders, an efficient destacker, safety fence, lubrication system and much more,” says Barvö.
Tomas Lidbacken is satisfied.
“The delivery and installation went entirely according to our agreed plan and without disruption. AP&T deserves a lot of credit.”
Facts
- PVI Esskå manufactures chassis and body parts for trucks. The company is located in Landeryd, Sweden and has approximately 60 employees.
- All of PVI Esskå’s hydraulic presses were supplied and installed by AP&T.
- In the summer of 2022, AP&T upgraded and future proofed one of the company’s press lines by rebuilding the control systems and installing new automation equipment.
- The investment reduced the line’s cycle times by about 50% and increased production capacity by about 500 hours/year.
Leave A Comment
You must be logged in to post a comment.