By linking to real production data, Schuler’s “Energy Monitor” enables savings of ten percent and more
Göppingen, October 19, 2022 – Electricity prices currently know only one direction: upward, and in vertical flight. So it’s definitely time to look around for ways to save energy in the press shop, too. Schuler’s “Energy Monitor”, which links information on the power consumption of a system including all its peripherals – such as the coil line or transfer – with the production data, provides important pointers. This makes it possible to see at a glance which die and which product, for example, has the highest energy requirement at which number of strokes.
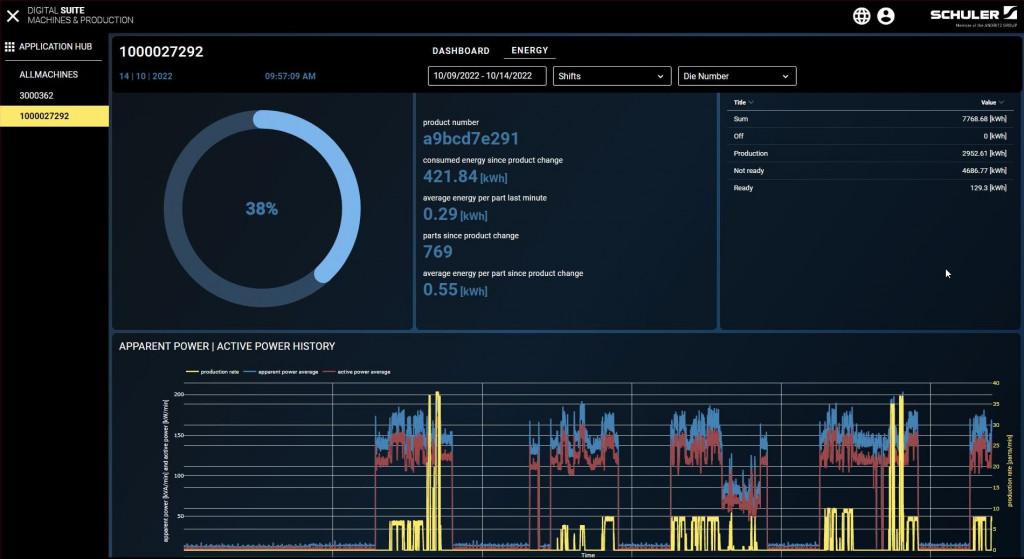
The Energy Monitor provides a detailed breakdown of a line’s electricity requirements and links this to production data. © Schuler
“Experience shows that customers save at least ten percent once they know the consuming devices in detail,” explains Andreas Banzhaf from Schuler Service. Realizing how many hours some presses are ready for operation but not producing can be an eye opener. It is not uncommon for lines to remain switched on over the weekend, drawing between 500 and 1,000 kilowatt hours, depending on their size, without a single part falling onto the outfeed conveyor.
“In addition, many automotive manufacturers now require their suppliers to provide precise information on energy consumption per component produced,” adds Andreas Banzhaf. This is exactly the information that the Energy Monitor calculates automatically. The prerequisite for this is the Production Monitor being already installed on the Schuler line. Both applications are part of the Digital Suite, which now bundles a whole range of solutions from the press manufacturer for networking forming technology. They can be accessed from any end device via digitalsuite.schulergroup.com.

The energy consumption per part now required by many car manufacturers is calculated automatically. © Schuler
The necessary measuring systems for the Energy Monitor are installed within a day and are already prepared for future functional expansions and updates. According to Andreas Banzhaf, the investment costs pay for themselves within a very short time: “Especially since energy prices are not expected to fall back to their previous levels in the foreseeable future.”
Schuler will present the “Energy Monitor” at the EuroBLECH trade fair in Hanover, Germany, from October 25 to 28 (Booth 27-G82).
Internet
Leave A Comment
You must be logged in to post a comment.