AP&T in Germany has received an order for the company’s patented solution for advanced partial press hardening – TemperBox®. The order also includes AP&T’s Multi-Layer Furnace, automation equipment, control system and integration. The equipment will be delivered, installed and commissioned this autumn.
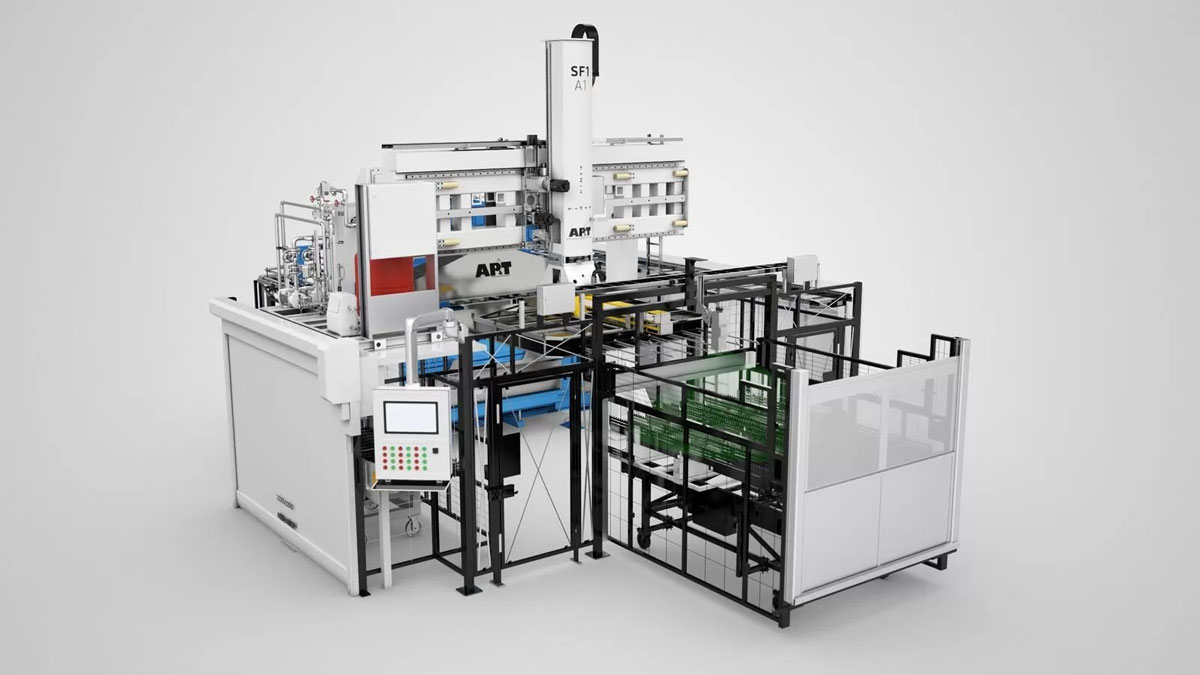
TemperBox® in a compact solution including AP&T’s Multi-Layer Furnace, automation equipment and control system.
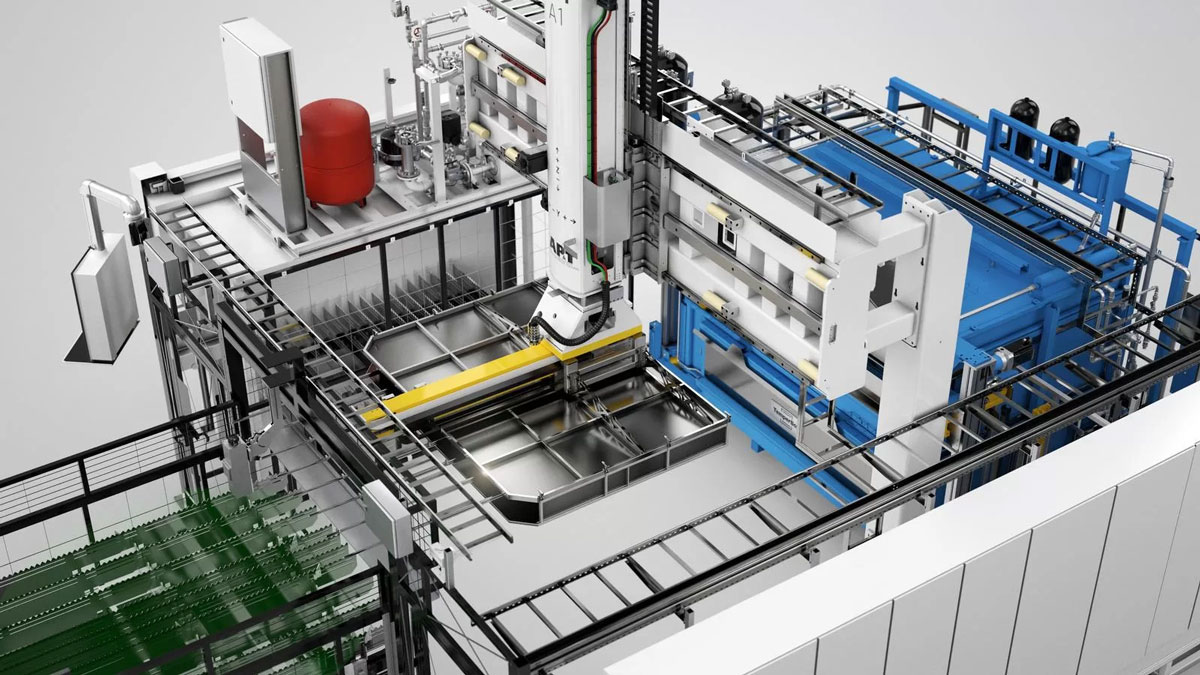
TemperBox® makes it possible to combine hard and soft zones in one and the same structural part, thereby creating new possibilities for innovative design, making the next generation of vehicles lighter and safer.
“TemperBox® makes it possible to combine hard and soft zones in one and the same structural part, thereby creating new possibilities for innovative design, making the next generation of vehicles lighter and safer. The fact that one of the world’s foremost automotive manufacturers – Mercedes-Benz in Sindelfingen – has now chosen our solution for partial press hardening as their technology of choice is certainly positive,” says Achim Krauß, Area Sales Manager at AP&T in Germany.
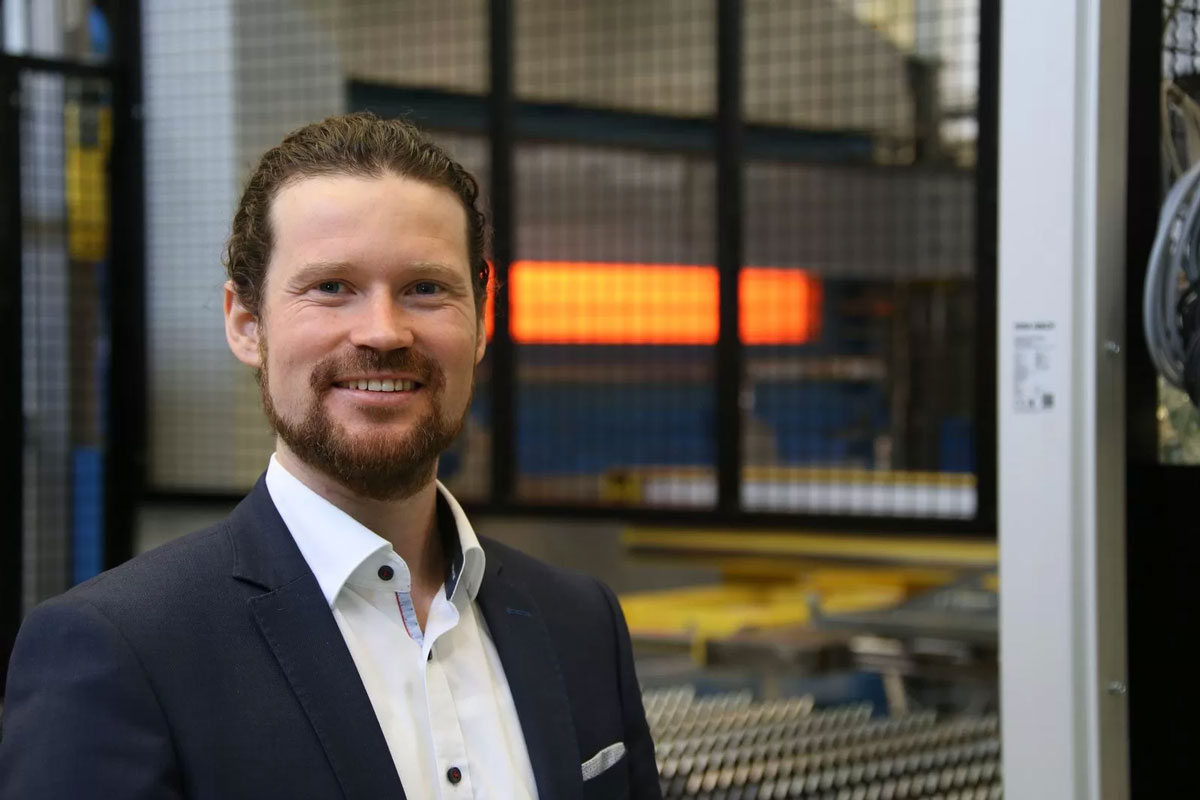
We are happy to announce that one of the world’s foremost automotive manufacturers has chosen our solution for partial press hardening as their technology of choice”, says Achim Krauß, Area Sales Manager at AP&T in Germany.
The TemperBox® will be used in test manufacturing a number of different parts, a process that demands flexibility.
AP&T’s innovative capabilities have been put to the test, even in the design of the physical installation. Part of the test was getting the equipment to fit into the limited space of the existing press area. AP&T’s Multi-Layer Furnace, one layer of which consists of the TemperBox® module, helped resolve the space issue.
The blank to be formed is transported from a loading station to one of the ‘usual’ furnace layers with the help of a four-axis SpeedFeeder. After being heated to about 900 degrees, the blank is transferred to the TemperBox®module for partial cooling. It then moves on to be fed and formed in the press tool.
“We have closely collaborated to design a solution that meets practical and technical needs and that will make a meaningful contribution to developing the vehicles of the future,” says Achim Krauß at AP&T.
Facts about TemperBox®
With TemperBox® individually defined areas of press hardened components can be fully hardened to maximize strength while the other individually defined areas remain soft. This is to achieve the desired ductility and/or to facilitate post processing such as joining or mechanical cutting, allowing designers and manufacturing engineers to work more freely without considering costly reinforcements, cycle time intensive hardening processes or other tailored solutions. TemperBox® is a fully commercial and globally available product, industrialized by AP&T together with Gedia.
Leave A Comment
You must be logged in to post a comment.